What is job costing in construction? This question comes up often when contractors start thinking about tracking profitability at the project level. Job costing is simply the process of tracking all expenses for a specific construction project. This includes labor, materials, equipment, and overhead costs.
Many contractors want to improve their profits but don’t know where their money goes. They win bids and work hard but wonder why projects don’t generate expected returns. Job costing provides the answer by showing exactly what each project costs to complete.
The good news is that job costing doesn’t require expensive software to get started. You can begin with basic tools like spreadsheets or even pen and paper. The key is developing a systematic process that captures all project costs accurately.
What Is Job Costing in Construction Fundamentals
What is job costing in construction at its core? Job costing tracks every dollar spent on a specific project from start to finish. This process separates costs by individual jobs rather than mixing all expenses together in general business accounts.
Traditional accounting methods show total business expenses but don’t reveal which projects make money and which ones lose money. Job costing solves this problem by assigning every cost to a specific project. This detailed tracking reveals true project profitability.
The job costing process involves three main steps. First, you establish cost categories that organize expenses logically. Second, you capture all costs as they occur during the project. Third, you analyze the data to understand project performance and improve future estimates.
This systematic approach works for construction companies of any size. Small contractors can use simple methods while larger companies might need more sophisticated systems. The principles remain the same regardless of company size or project complexity.
Construction Job Costing Overview
Construction job costing faces unique challenges that don’t exist in other industries. Projects happen at different locations with changing crews and variable material costs. Weather delays, scope changes, and complex subcontractor arrangements add complexity.
Each construction project is essentially a temporary business with its own income and expenses. Unlike manufacturing where products are identical, every construction job has unique requirements and challenges. This uniqueness makes accurate cost tracking essential.
Construction job costing must account for both direct costs that can be traced to specific projects and indirect costs that support multiple projects. Direct costs include labor, materials, and equipment used exclusively on one job. Indirect costs include office expenses, insurance, and administrative salaries.
The goal is to understand the complete cost picture for each project. This information helps with pricing future work, managing current projects, and making strategic business decisions. Without accurate job costing, contractors operate with incomplete financial information.
Project timing adds another layer of complexity. Construction projects often span several months with costs occurring at different phases. Materials might be delivered early while labor costs happen throughout the project. Equipment might be needed only during specific phases.
Calculate Job Costing Step by Step
Calculate job costing by following a systematic process that captures all project expenses. Start by establishing cost categories that make sense for your type of work. Most contractors use categories like labor, materials, equipment, subcontractors, and overhead.
Create a simple tracking system using spreadsheets or paper forms. List your cost categories across the top and record expenses as they occur. Include the date, description, amount, and cost category for each expense. This basic system provides the foundation for accurate job costing.
Track labor costs by recording hours worked and applying appropriate wage rates. Include not just base wages but also payroll taxes, insurance, and benefits. These burden costs typically add 25-40% to base wages and must be included for accurate job costing.
Record material costs when materials are delivered to the job site. Include the purchase price plus any delivery charges or sales taxes. Track waste and leftover materials to understand true material consumption. This information helps improve future material estimates.
Equipment costs include both rental charges and costs for company-owned equipment. Calculate hourly rates for owned equipment based on depreciation, maintenance, and operating costs. Track actual hours of use to assign appropriate equipment costs to each project.
Quick tip: Most construction companies find that burden costs (taxes, insurance, benefits) add 30-35% to direct labor wages, so always include these when calculating true labor costs.
Construction Industry Cost Tracking
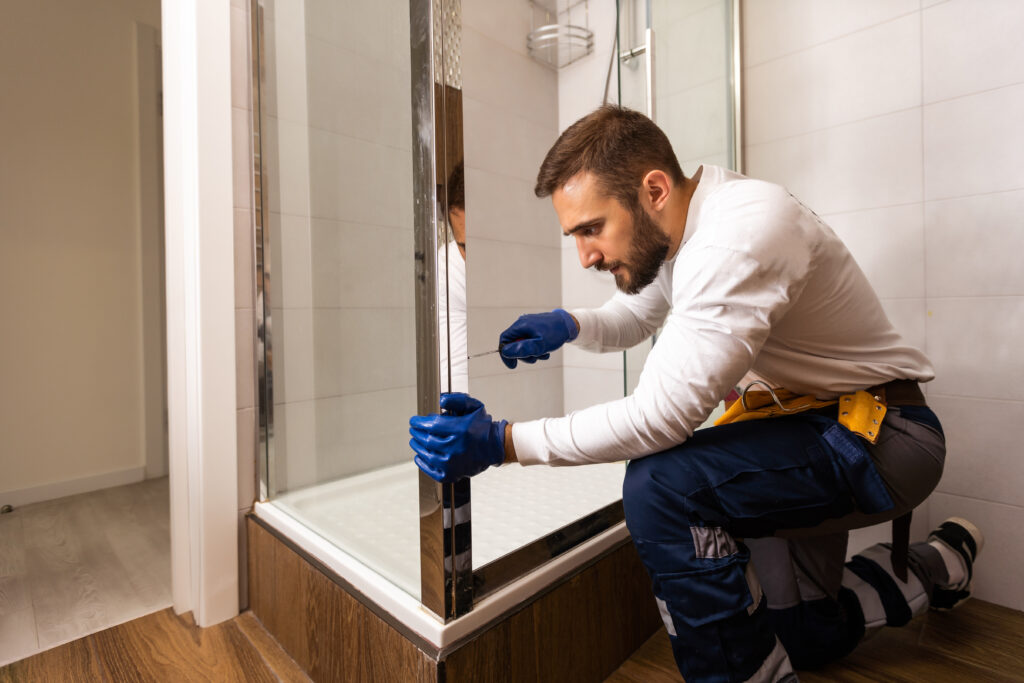
Young plumber fixing shower cabin.
The construction industry requires specialized cost tracking methods that account for project-based work and complex cost structures. Standard business accounting methods don’t provide the detail needed for construction project management.
Manufacturing companies make identical products with predictable costs. Service businesses have consistent processes with stable pricing. Construction projects are unique with variable costs that depend on site conditions, weather, and client requirements.
Construction industry regulations add compliance costs that must be tracked and allocated properly. Certified payroll requirements, safety regulations, and environmental compliance create administrative expenses. These costs affect project profitability and must be included in job costing.
The industry’s competitive bidding environment makes accurate cost data essential for pricing decisions. Contractors who understand their true costs can bid more competitively while maintaining profit margins. Those without accurate data often win work at unprofitable prices.
Seasonal variations affect construction costs throughout the year. Winter work might require heating and additional labor. Summer projects might face material shortages and premium pricing. Job costing helps track these seasonal cost patterns and improve future planning.
Subcontractor coordination creates additional cost tracking challenges. Multiple trades working on the same project require careful coordination and cost allocation. Job costing software systems must track subcontractor performance and costs to optimize future subcontractor selection.
Construction Job Categories
Construction job categories help organize projects for better cost tracking and analysis. Different types of work have different cost patterns and profitability characteristics. Understanding these differences helps improve estimating and project management.
Residential construction typically involves smaller projects with shorter durations. Material costs might represent a larger percentage of total costs while labor productivity varies based on crew experience. These projects often have simpler cost structures but require attention to detail.
Commercial construction jobs are usually larger with more complex requirements. These projects might involve multiple phases with different cost characteristics. Office build-outs have different cost patterns than warehouse construction or retail spaces.
Industrial construction involves specialized equipment and materials with unique safety requirements. These projects often require certified workers and specialized equipment. The cost patterns differ significantly from residential or commercial work.
Infrastructure projects like roads, bridges, and utilities have their own unique cost characteristics. These projects often involve extensive earthwork, specialized materials, and complex logistics. Weather sensitivity can significantly impact costs and schedules.
Renovation and remodeling work presents special challenges for job costing. Existing conditions might be unknown until work begins. Demolition costs can vary significantly based on what’s discovered during the project. These uncertainties make accurate estimating difficult.
Construction Project Cost Elements
Construction project cost elements fall into several main categories that form the foundation of any job costing system. Understanding these categories helps ensure that all costs are captured and allocated properly.
Direct labor costs include wages for workers who perform project tasks. This category includes carpenters, electricians, plumbers, and other skilled trades. Calculate total labor costs by multiplying hours worked by wage rates plus burden costs.
Direct material costs cover all materials that become part of the finished project. This includes lumber, concrete, steel, electrical components, and plumbing fixtures. Track material costs from purchase through installation, including waste and leftover materials.
Equipment costs encompass both rental equipment and company-owned tools and machinery. Calculate costs based on actual usage hours and appropriate hourly rates. Include fuel, maintenance, and transportation costs when equipment moves between projects.
Subcontractor costs represent payments to independent contractors who perform specialized work. These costs are usually straightforward to track since they come from invoices. Ensure that all subcontractor change orders are captured and allocated properly.
Indirect costs support projects but can’t be traced to specific jobs. Office rent, utilities, insurance, and administrative salaries fall into this category. These costs are typically allocated to projects based on direct labor hours or total direct costs.
Accurate Job Costing Methods
Accurate job costing requires systematic methods that capture all costs consistently. Develop standardized procedures that everyone follows to ensure data quality and completeness.
Time tracking forms the foundation of accurate labor cost allocation. Require workers to record start and stop times for each project. Use time cards, mobile apps, or simple paper forms to capture this information daily. Weekly summaries help verify accuracy.
Receipt management ensures that all material and equipment costs are captured. Require receipts for all purchases and assign them to appropriate projects immediately. Develop a filing system that makes receipts easy to find for later reference.
Cost coding assigns expenses to appropriate categories for analysis and reporting. Establish a simple coding system that workers can understand and use consistently. Provide training to ensure that everyone codes expenses the same way.
Regular reconciliation compares tracked costs to bank statements and credit card bills. This process helps identify missed expenses and correct errors. Monthly reconciliation prevents small problems from becoming major discrepancies.
Documentation standards ensure that all cost information is recorded completely and accurately. Include project name, date, description, and cost category for every expense. This documentation supports analysis and provides audit trails for verification.
Construction Business Financial Control
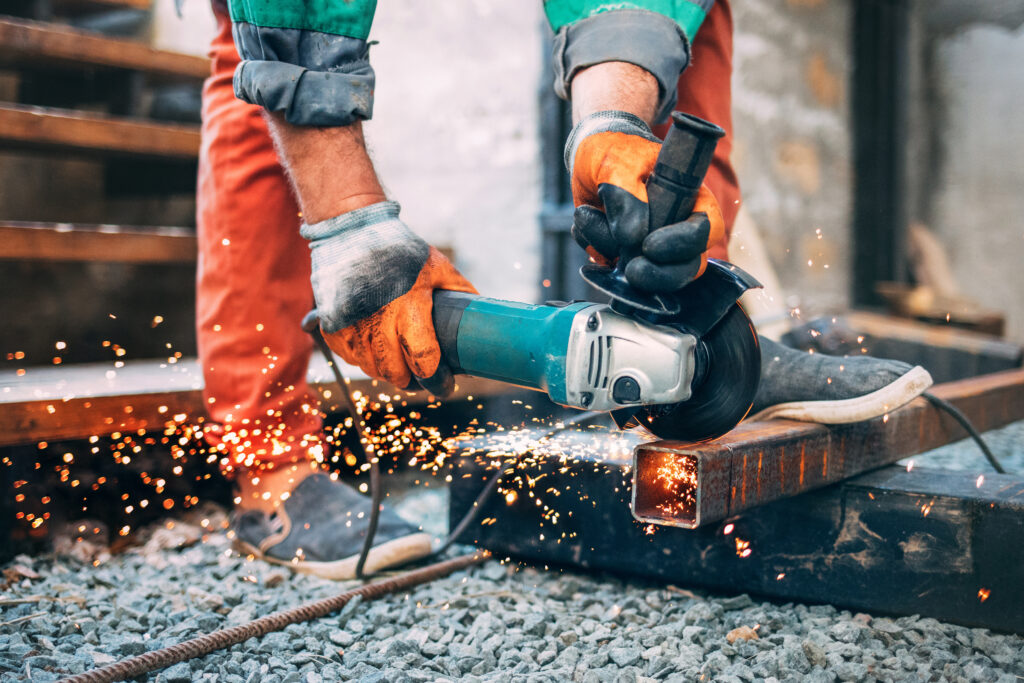
a man is sawing metal with an angle grinder. Sparks, close up
Construction business financial control depends on accurate job costing that provides real-time visibility into project performance. This control helps prevent cost overruns and protects profit margins.
Project budget monitoring compares actual costs to estimated costs throughout the project lifecycle. Weekly reviews help identify problems early when corrective action is still possible. This proactive approach prevents small issues from becoming major losses.
Cash flow management benefits from understanding when project costs will occur. Job costing helps predict cash needs and identify billing opportunities. This information helps maintain adequate working capital for business operations.
Profit margin protection requires understanding all costs that affect project profitability. Job costing reveals hidden costs that might not be obvious without systematic tracking. This visibility helps make pricing decisions that protect margins.
Performance measurement uses job costing data to evaluate project and company performance. Compare actual costs to estimates to identify areas for improvement. Track trends over time to measure progress and identify successful practices.
Decision making improves when managers have accurate cost information. Resource allocation, pricing decisions, and project management all benefit from reliable job costing data. This information helps optimize business operations and improve profitability.
Cost Codes and Organization
Cost codes provide the organizational structure that makes job costing data useful for analysis and decision making. Well-designed cost codes make it easy to track expenses and generate meaningful reports.
Standardized cost codes ensure consistent data entry across all projects and all team members. Most construction companies use industry-standard coding systems that organize costs by work type and expense category. This standardization enables comparison across projects.
Hierarchical cost codes allow reporting at different levels of detail. High-level codes might separate labor, materials, and equipment while detailed codes break down specific trades and material types. This flexibility supports different reporting needs.
Simple cost codes work better than complex systems that confuse users. Most successful systems use 3-5 digit codes that are easy to remember and apply. Complex coding systems often lead to errors and inconsistent usage.
Cost code training ensures that all team members understand how to use the coding system properly. Provide clear definitions and examples for each code. Regular training sessions help maintain consistency and accuracy.
Cost code maintenance keeps the system current with business needs. Add new codes when needed and retire codes that are no longer used. Regular review ensures that the coding system continues to meet business requirements.
Did you know? Construction companies using standardized cost codes report 40% better accuracy in project cost analysis compared to companies with inconsistent coding practices.
Process Costing vs Job Costing
Process costing and job costing represent two different approaches to cost accounting. Understanding the difference helps construction companies choose the right method for their business model.
Process costing works well for companies that produce identical products or services. Manufacturing companies often use process costing because they make the same products repeatedly. Costs are averaged across all units produced during a specific period.
Job costing tracks costs for specific projects or jobs. Each project is treated as a separate cost object with its own income and expenses. This method works well for construction because every project is unique with different requirements and challenges.
Construction companies might use elements of both methods depending on their business model. Companies that build identical homes might use process costing for standard features while using job costing for custom elements. Most construction work requires job costing due to project uniqueness.
Hybrid approaches combine elements of both methods to optimize cost tracking. Standard processes might use predetermined rates while unique work gets tracked individually. This approach can simplify administration while maintaining accuracy.
The choice between methods depends on business model, project types, and reporting requirements. Most construction companies find that job costing provides better information for decision making and profitability analysis.
Cash Flow Impact
Cash flow management is critical for construction business success. Job costing provides the information needed to predict cash needs and optimize cash flow timing.
Revenue timing in construction often doesn’t match cost timing. Materials might be purchased before work begins while labor costs occur throughout the project. Equipment might be needed only during specific phases. This timing mismatch affects cash flow.
Progress billing requires accurate tracking of work completed. Job costing helps determine when billing milestones are reached and how much work has been accomplished. This information enables prompt billing that improves cash flow.
Cost forecasting uses job costing data to predict future cash needs. Understanding cost trends helps estimate remaining expenses and plan cash requirements. This forecasting helps avoid cash shortages that can disrupt operations.
Working capital optimization reduces the cash required to fund operations. Job costing helps identify opportunities to accelerate billing and optimize payment timing. This optimization reduces the cash required to support business growth.
Payment scheduling coordinates cash receipts with cash disbursements. Job costing helps predict when major expenses will occur and when customer payments will arrive. This coordination helps maintain adequate cash balances.
Seasonal planning uses job costing data to understand how business patterns affect cash flow. Construction activity often varies by season with corresponding changes in cash requirements. Historical job costing data helps plan for these variations.
Construction Accounting Software Benefits
Construction accounting software provides specialized capabilities that general business software lacks. These systems are designed specifically for construction industry requirements and job costing needs.
Project-based accounting organizes all financial information by individual jobs rather than general business categories. This organization provides the detail needed for accurate job costing and project profitability analysis.
Automated cost allocation reduces manual data entry and improves accuracy. Time tracking integrates with payroll while purchase orders flow to job costing automatically. This automation ensures that all costs are captured and allocated properly.
Real-time reporting provides current information for decision making. Dashboards show project costs and budget variances as they occur. This immediate feedback allows quick responses to problems and opportunities.
Industry-specific features handle construction requirements like certified payroll, union reporting, and retention management. These capabilities are essential for construction businesses but unavailable in general business software.
Mobile capabilities allow field teams to enter data from job sites. Time tracking, expense reporting, and progress updates can be done from smartphones and tablets. This mobility improves data accuracy and reduces administrative overhead.
Integration capabilities connect job costing with other business systems. Accounting, project management, and estimating software can share data automatically. This integration eliminates duplicate data entry and ensures consistency across all systems.
Accounting Software Selection
Accounting software selection for construction companies requires careful consideration of industry-specific needs and job costing requirements. The right software provides the foundation for effective financial management.
Feature requirements include project-based accounting, job costing capabilities, and construction-specific reporting. The software should handle certified payroll, retention management, and union reporting if needed. Mobile capabilities are increasingly important for field data collection.
Scalability ensures that software grows with the business. Small companies might start with basic features but need the ability to add capabilities as they expand. Choose software that can handle increasing project volumes and complexity.
Integration capabilities connect the accounting software with other business systems. Job costing should integrate with estimating, project management, and scheduling software. These connections eliminate duplicate data entry and improve data consistency.
User experience affects adoption rates and system effectiveness. Choose software with intuitive interfaces that field and office staff can use effectively. Complex systems often fail because users find them difficult to navigate.
Support and training help ensure successful implementation. Look for vendors that provide comprehensive training and ongoing support. Construction software often requires specialized knowledge that vendors should provide.
Cost considerations include both initial licensing and ongoing support costs. Compare total cost of ownership rather than just initial purchase prices. Consider the value provided relative to the cost of implementation and operation.
Quick tip: Construction businesses that choose accounting software specifically designed for their industry typically achieve 60% faster implementation and 25% better user adoption rates.
Learning from common mistakes helps improve job costing accuracy and effectiveness. Understanding typical pitfalls helps contractors avoid expensive errors that can impact profitability. Check out Common Job Costing Mistakes (and How to Avoid Them) for detailed guidance.
Implementing job costing doesn’t require expensive software to get started. Many contractors successfully track costs using basic tools and systematic processes. Learn practical implementation strategies in How to Implement Job Costing on Construction Projects (Even Without Software)
For contractors ready to invest in specialized software, comprehensive guidance is available in The Ultimate Guide to Job Costing Software for Construction which compares options and features.
The Construction Industry Institute provides additional research and resources on construction project management best practices that complement effective job costing implementation.
Frequently Asked Questions
How can Projul help contractors who are new to job costing?
Projul simplifies job costing for contractors who are just getting started with automated data collection and intuitive interfaces. Our system guides users through proper cost coding and provides real-time feedback on data quality. New users typically achieve 90% cost tracking accuracy within their first week of using Projul, compared to months of learning with manual systems.
Can Projul work for contractors currently using spreadsheets or paper-based tracking?
Yes, Projul seamlessly transitions contractors from manual systems to automated job costing. We can import existing spreadsheet data and provide migration assistance to ensure no historical information is lost. Our mobile apps replace paper timesheets while maintaining familiar workflows that field teams can adopt quickly.
How does Projul handle both direct and indirect cost allocation?
Projul automatically calculates and allocates indirect costs using customizable overhead rates based on your business model. The system tracks direct costs in real-time while applying appropriate overhead allocations to provide complete project cost visibility. This automation ensures accurate job costing without complex manual calculations.
What training and support does Projul provide for job costing implementation?
Projul includes comprehensive training programs designed specifically for construction teams new to systematic job costing. We provide step-by-step guidance on setting up cost codes, training field staff, and interpreting reports. Our support team includes construction industry experts who understand the unique challenges contractors face.
How quickly can contractors see results from implementing Projul for job costing?
Most contractors see immediate improvements in cost tracking accuracy and project visibility within one week of implementing Projul. Meaningful profitability improvements typically appear within 30-60 days as better cost data leads to improved decision making. The system pays for itself through better cost control and more accurate estimating.
Does Projul integrate with existing accounting software for seamless job costing?
Projul integrates with popular construction accounting software including QuickBooks, Sage, and Foundation. These integrations ensure that job costing data flows automatically to financial statements while eliminating duplicate data entry. The seamless connection provides complete financial visibility across all business systems.
Starting Your Job Costing Journey
Construction job costing doesn’t have to be complicated to be effective. The most important step is to start tracking costs systematically, even if you begin with simple tools. Discipline and consistency matter more than sophisticated software when you’re getting started.
Many successful construction businesses began their job costing journey with basic spreadsheets or paper forms. The key is developing good habits around cost tracking and data collection. These habits become the foundation for more sophisticated systems as your business grows.
Technology can enhance construction job costing effectiveness, but it’s not required to get started. Focus on establishing clear processes and training your team to follow them consistently. Once these foundations are in place, software can automate and improve your existing processes.
The investment in job costing pays dividends through better project management, improved estimating, and higher profit margins. Companies that track job costs consistently achieve better financial results than those that operate without this visibility.
Your construction business deserves the financial clarity that comes from understanding what each project actually costs. Start with simple methods and build your capabilities over time. The journey toward better job costing begins with a single step toward systematic cost tracking.